In our previous article, we celebrated the rise of sintered stone, a revolutionary material that has taken the architectural industry by storm. As the demand for this exceptional material continues to soar, manufacturers are exploring more efficient and innovative production methods.
Now, in this article, we will take an in-depth look at the groundbreaking advancements made in sintered stone production, with a particular focus on SACMI Continua+ technology. This transition from traditional hydraulic press technology to the cutting-edge continuous compaction technique has been a game-changer, elevating the industry’s efficiency and overall excellence in manufacturing.
The traditional method of producing sintered stone using hydraulic presses served as the industry standard for years. China has been a significant contributor to the global sintered stone market, with several manufacturers adopting innovative techniques to produce high-quality materials. Chinese technology has played a crucial role in advancing sintered stone production and expanding its applications. The System Pressing Machine represents a fusion of traditional compaction and pressing techniques with modern automation and precision. It is suitable for smaller-scale production runs, allowing manufacturers to efficiently cater to diverse project needs. It also is an excellent option for manufacturers seeking precision molding, custom sizes, and cost-effectiveness. However, this landscape changed dramatically with the advent of SACMI Continua+.

(SYSTEM photo from Internet)
The revolutionary Continua+ technology introduced by SACMI, an esteemed multinational company based in Italy, has transformed the sintered stone industry by enabling a continuous compaction process. This innovative approach moves away from the limitations of batch production, ushering in a new era of possibilities and making it a game-changer in the industry.
At the core of this groundbreaking technology lies the PCR (Roller Compactor Press), a machine that compacts incoming powder layers using two motorized belts with converging axes and intermediate drive rollers. These belts, driven by electronic speed control, boast adjustable compaction geometry, offering enhanced flexibility in the production process. The compactor body itself facilitates easy replacement of the upper belt by opening one side of the machine and using pneumatic cylinders to lift and position the belt.
The adoption of SACMI Continua+ technology has introduced several advantages that have contributed to its widespread adoption in the sintered stone industry:
1. Speed and Efficiency: Continua+ technology streamlines the manufacturing process, reducing production time and increasing overall efficiency. Manufacturers can now produce sintered stone slabs continuously, significantly increasing output without compromising quality.
2. Design Flexibility: The continuous compaction process allows for greater design flexibility. Intricate patterns, textures, and varying thicknesses can be seamlessly integrated into the production process, enabling architects and designers to explore creative possibilities like never before.
3. Superior Product Quality: The elimination of intermediate drying stages ensures better material homogeneity and structural integrity. SACMI Continua+ delivers consistent and high-quality sintered stone slabs, meeting the stringent demands of modern architectural projects.
Moreover, SACMI Continua+ technology offers notable environmental benefits, reducing energy consumption and minimizing waste compared to traditional methods. This sustainable approach aligns with the industry’s growing emphasis on eco-friendly practices.
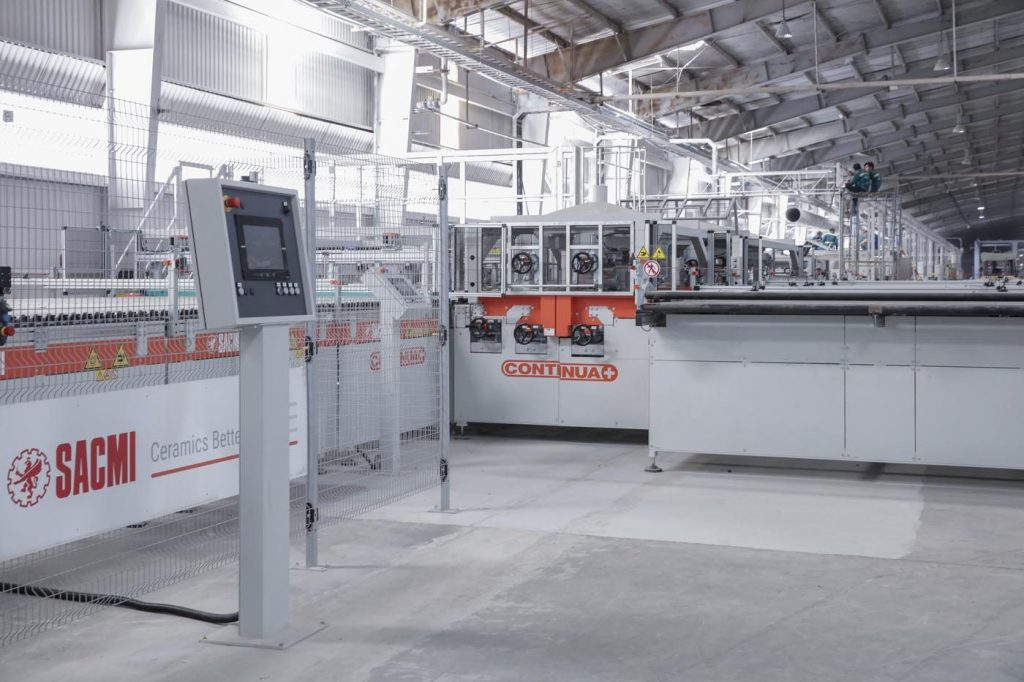
(Bach Ma photo: Real-world examples showcase the success of SACMI Continua+ technology in architectural projects. One such example is Vasta Stone, Vietnam’s first luxury sintered stone brand, which employs Continua+ technology to redefine the landscape of architectural materials with its unmatched quality and sophistication.)
While SACMI Continua+ technology brings numerous advantages, it is essential to address potential challenges as well. Manufacturers may face initial investment costs and the need for specialized training to operate and maintain the continuous compaction process effectively. However, the long-term benefits far outweigh these challenges, making it a worthwhile investment for the industry’s future.
In conclusion, the transition from traditional hydraulic press technology to SACMI Continua+ continuous compaction has marked a turning point in the sintered stone industry. With its remarkable speed, design flexibility, superior product quality, and sustainability aspects, Continua+ technology has become a driving force behind the industry’s growth and success. As the industry continues to evolve, SACMI Continua+ technology will undoubtedly remain at the forefront of innovation, inspiring new possibilities for architects, designers, and manufacturers alike.